The cost of quality in the language of the United Kingdom often referred to with the Quality Costs are costs incur in handling the issue of quality (Quality), in either order improve quality or costs incur due to poor quality (Cost of Poor Quality). In other words, the cost of Quality are all costs that arise in quality management (Quality Management).
"Total Quality Control" mentions that Quality consists of 3 main categories, namely the cost of Prevention (Preventive Cost), the cost assessment (Appraisal Cost) cost of failure (Failure Cost). The cost of Failure is then further divide into 2 types i.e. Internal Failure Costs (Internal Failure Cost) and External Failure Costs (External Failure Cost).
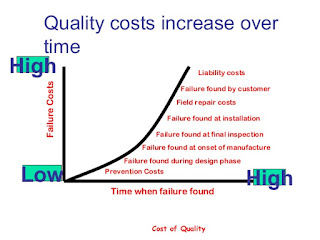
The cost of Prevention (Preventive Cost) is the cost incur in preventing failure occur on the first process. Such as the cost of Training (Training Cost) and cost Planning Quality (Quality Planning). Appraisal Cost is the cost incur while conducting screening or detection of the failure of the product. Such as the cost of testing, inspection and Audit process.
While the cost of Failure is the cost incur due to poor quality or failure of products. That don't meet the standards of the customer (Customer). In the cost of this failure, there is again an Internal failure costs incur as a result of poor quality during the production process. External Failure Costs incur as a result of the failure of a product that have been sold.
For more details, please look at the table below concerning the 3 main categories of cost of Quality (Quality Cost) along with an example of the costs that would arise from the Costs of such Quality.
Cost of Poor Quality (COPQ) is the cost incur due to poor quality or failure of products. That don't meet the standards of the customer (Customer). The company was able to improve its quality and elimination occurs. It will cost COPQ can increase the Profits of the company. So that it has an advantage in competing with its competitors.
The costs incur due to poor Quality not just 3 main categories mention above. But there is also a loss-loss or other hidden costs (Hidden cost) as in loss due to lost Business. Costs of projects/ Management, loss of customer trust, the cost of lost assets and so on. These costs is like an iceberg which is insubstantial in the surface of the water is less compare to that hidden in the water.
One of the strategies use by company management to elimination COPQ (Cost of Poor Quality). It is to implement the Six Sigma Methodology. With Six Sigma Management companies are able to identify. The causes of the occurrence of the failure and doing improvements to enhance the overall Quality.
"Total Quality Control" mentions that Quality consists of 3 main categories, namely the cost of Prevention (Preventive Cost), the cost assessment (Appraisal Cost) cost of failure (Failure Cost). The cost of Failure is then further divide into 2 types i.e. Internal Failure Costs (Internal Failure Cost) and External Failure Costs (External Failure Cost).
The cost of quality is generally classify into four categories:
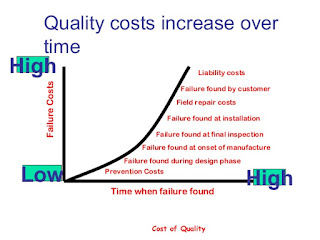
- External Failure Cost: Cost associate with defects found after the customer receives the product or service. Example: Processing customer complaints, customer returns, warranty claims, product recalls.
- Internal Failure Cost: Cost associate with defects found before the customer receives the product or service. Example: Scrap, rework, re-inspection, re-testing, material review, material downgrades
- Inspection (appraisal) Cost: Cost incur to determine the degree of conformance to quality requirements (measuring, evaluating or auditing). Example: Inspection, testing, process or service audits, calibration of measuring and test equipment.
- Prevention Cost: Cost incur to prevent (keep failure and appraisal cost to a minimum) poor quality. Example: New product review, quality planning, supplier surveys, process reviews, quality improvement teams, education and training.
Introduction
The cost of Prevention (Preventive Cost) is the cost incur in preventing failure occur on the first process. Such as the cost of Training (Training Cost) and cost Planning Quality (Quality Planning). Appraisal Cost is the cost incur while conducting screening or detection of the failure of the product. Such as the cost of testing, inspection and Audit process.
While the cost of Failure is the cost incur due to poor quality or failure of products. That don't meet the standards of the customer (Customer). In the cost of this failure, there is again an Internal failure costs incur as a result of poor quality during the production process. External Failure Costs incur as a result of the failure of a product that have been sold.
Major Categories
For more details, please look at the table below concerning the 3 main categories of cost of Quality (Quality Cost) along with an example of the costs that would arise from the Costs of such Quality.
Category | Examples of Costs that need to be issue |
The Cost Of Prevention (Preventive Cost) | 1. The cost of Training (Training Cost) 2. Process Capability Studies (Research Capability of the process) 3. Vendor Survey 4. Quality Planning and Design |
The Cost Assessment (Appraisal Cost) | 1. All types of testing (testing) and inspection 2. Purchase of equipment Testing and inspection 3. Review the quality and Audit (Audit and Review) 4. Laboratory Fee |
The Cost Of Failure (Failure Cost) Internal | 1. The cost of Scrap and rework (Rework) 2. The cost of design changes (Design Change) 3. The cost of preparation of Excess (Excess Inventory Cost) 4. The cost of purchasing Materials |
The Cost Of Failure (Failure Cost) External | 1. Cost of Sales/Warranty (Warranty) 2. Costs of return of the product (Return and Recall) 3. The cost of Handling customer complaints 4. The cost of Indemnification |
Costs due to bad quality/Cost of Poor Quality (COPQ)
Cost of Poor Quality (COPQ) is the cost incur due to poor quality or failure of products. That don't meet the standards of the customer (Customer). The company was able to improve its quality and elimination occurs. It will cost COPQ can increase the Profits of the company. So that it has an advantage in competing with its competitors.
The costs incur due to poor Quality not just 3 main categories mention above. But there is also a loss-loss or other hidden costs (Hidden cost) as in loss due to lost Business. Costs of projects/ Management, loss of customer trust, the cost of lost assets and so on. These costs is like an iceberg which is insubstantial in the surface of the water is less compare to that hidden in the water.
One of the strategies use by company management to elimination COPQ (Cost of Poor Quality). It is to implement the Six Sigma Methodology. With Six Sigma Management companies are able to identify. The causes of the occurrence of the failure and doing improvements to enhance the overall Quality.
No comments:
Post a Comment